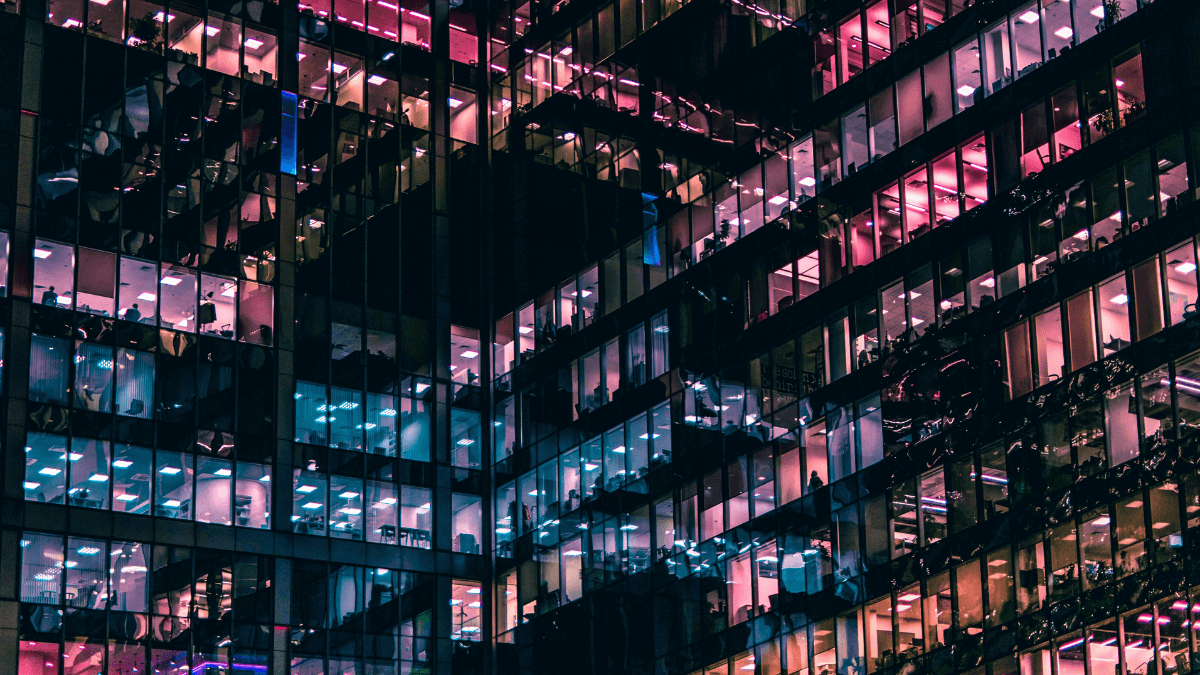
Optimizing operations for maximum efficiency is crucial for success. Lean management principles, originally developed in the manufacturing industry, have proven to be highly effective in various sectors, from healthcare to service industries. By adopting lean management techniques, businesses can eliminate waste, streamline processes, and enhance overall productivity. This blog post explores the key concepts of lean management and provides practical steps for implementing these principles within your organization.
Understanding Lean Management
Lean management is a systematic approach to identifying and eliminating waste while delivering value to customers. Waste, in this context, refers to any activity or process that does not add value from the customer's perspective. The core principles of lean management include:
- Value: Define value from the customer's viewpoint and focus on what they truly need and are willing to pay for.
- Value Stream: Map out the value stream to identify all the steps involved in delivering the product or service. This helps pinpoint areas of waste.
- Flow: Ensure that the processes flow smoothly without interruptions or delays, creating a seamless production or service delivery line.
- Pull: Implement a pull-based system where production is based on customer demand rather than forecasting, minimizing overproduction and inventory.
- Perfection: Continuously strive for perfection by regularly reviewing and improving processes to enhance efficiency and meet customer expectations.
Steps to Implement Lean Management
1. Assess Current Processes
Begin by thoroughly analyzing your existing processes to identify areas of waste and inefficiency. This can be done through value stream mapping, where each step of a process is documented to highlight non-value-adding activities.
2. Engage Employees
Lean management thrives on the active participation of employees at all levels. Encourage a culture of continuous improvement by involving staff in identifying problems and brainstorming solutions. Offer training and resources to help them understand lean principles and how to apply them.
3. Eliminate Waste
Identify the types of waste present in your processes, such as overproduction, waiting times, excessive transportation, or defects. Implement strategies to eliminate or reduce these wastes, thus streamlining operations. Techniques such as the 5S (Sort, Set in order, Shine, Standardize, Sustain) methodology can help maintain an organized and efficient workspace.
4. Implement a Pull System
Shift from a push-based system, where products or services are created based on forecasts, to a pull-based system driven by actual customer demand. This approach minimizes excess inventory and ensures that resources are used more effectively.
5. Foster Continuous Improvement
Establish a culture of continuous improvement (Kaizen) where employees are encouraged to suggest and implement incremental changes regularly. Conduct regular meetings and workshops to review progress and identify new improvement opportunities.
Benefits of Lean Management
Implementing lean management principles can yield numerous benefits for your business, including:
- Enhanced Productivity: Streamlined processes result in faster and more efficient operations.
- Cost Savings: Reducing waste and improving resource utilization lower operational costs.
- Improved Quality: A focus on value and continuous improvement enhances product and service quality.
- Higher Employee Engagement: Involving employees in the improvement process boosts morale and job satisfaction.
- Increased Customer Satisfaction: Faster, more consistent service delivery leads to happier customers.
Lean management is more than just a set of tools; it is a holistic approach to running a business focused on delivering maximum value to customers while minimizing waste. By embracing lean principles, businesses can achieve significant improvements in efficiency, quality, and customer satisfaction. Begin your lean management journey today and unlock the full potential of your organization's operations.